Home Energy Audit Chicago
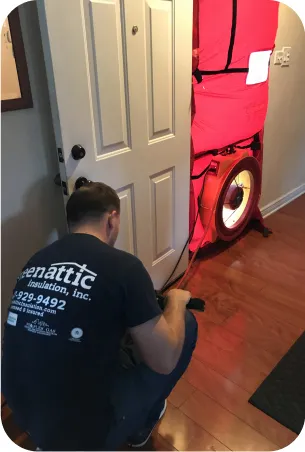
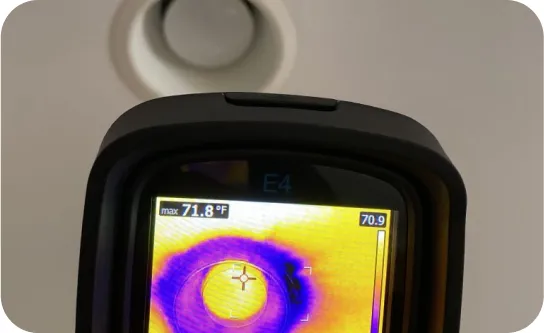
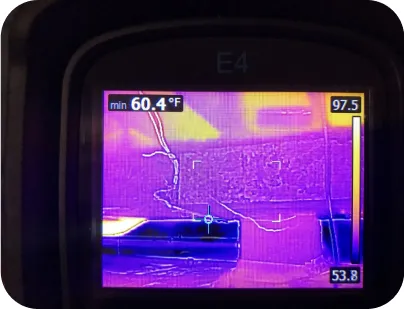
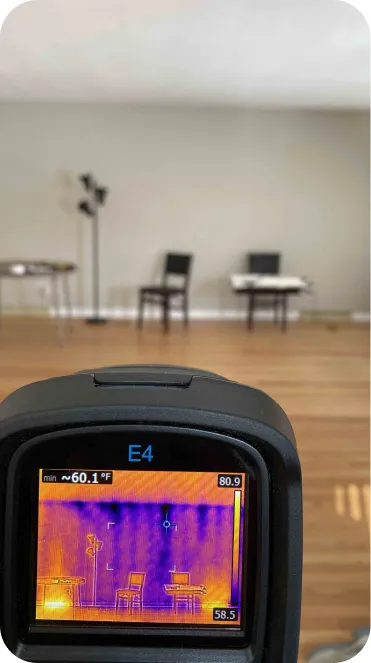
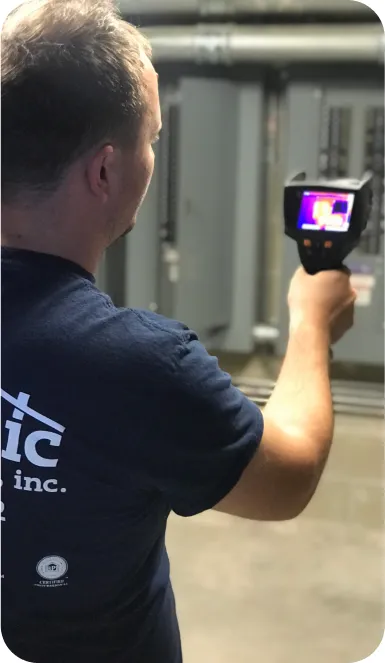
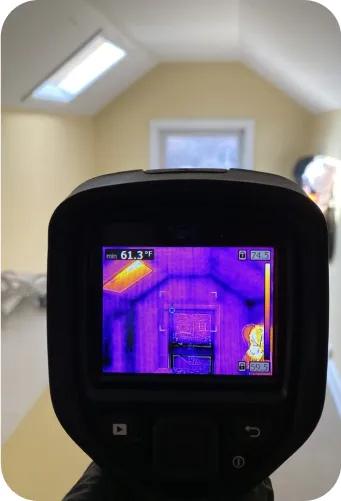
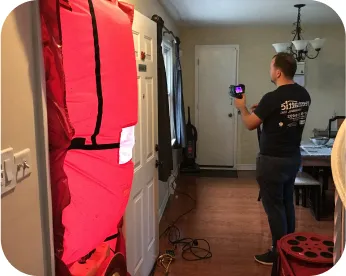
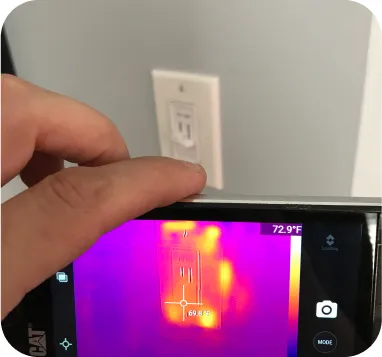
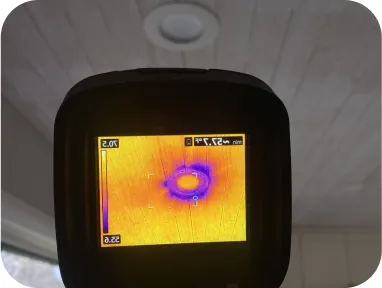
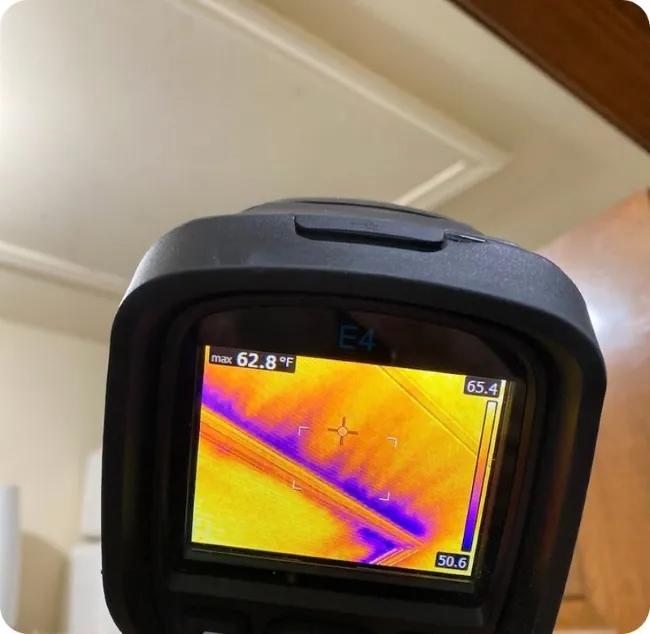
Energy Audit Chicago: Thermal Scan and Blower Door Test
Infrared Camera Scan or thermographic inspection, uses infrared imaging to detect temperature variations. It's used in buildings to spot heat loss, moisture intrusion, and inadequate insulation, assisting in diagnosing potential problems effectively.
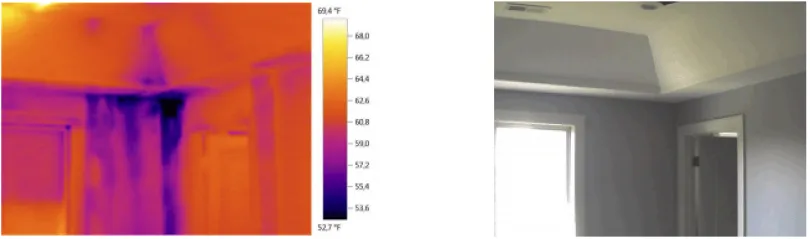
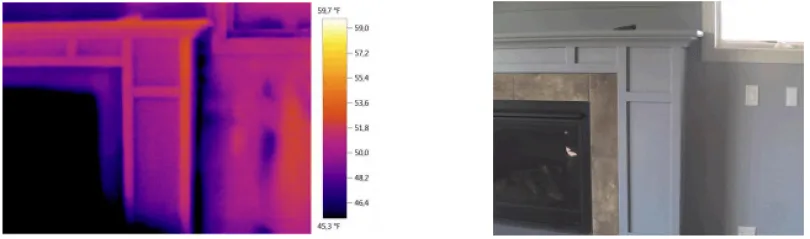
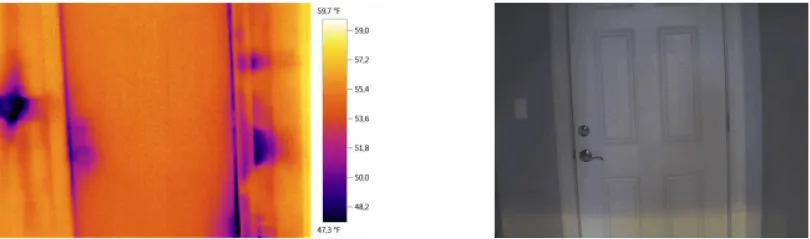
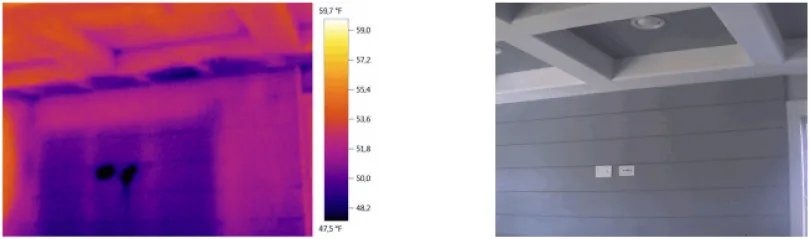
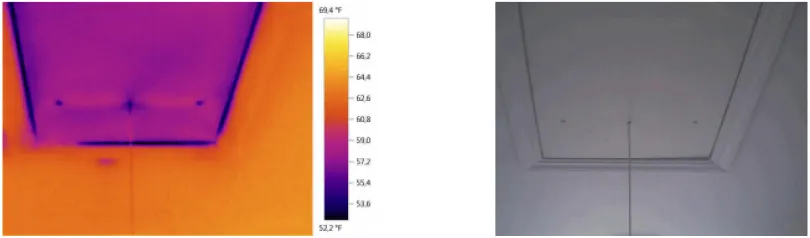
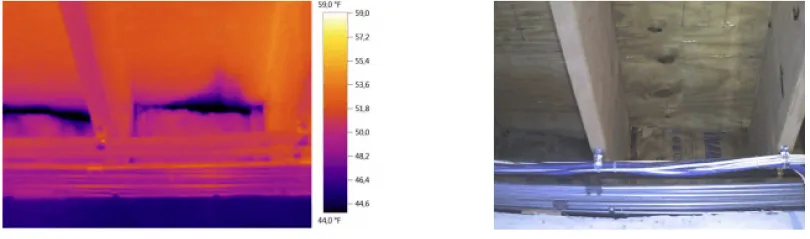
How to Find Cold / Hot Spots In House
Our technician can graphically display and photograph the insulation levels and cold or hot spots within your walls, ceiling, floors without creating any holes. Most people are amazed when they see a vivid image of where they aremissing insulation and what that does for heat loss in the winter or heat gain in the summer. Making the invisible visible.
Minimum Ventilation Requirements (MVR):
In order to maintain acceptable indoor air quality, some fresh air is required. In leaky homes this is easily accomplished through the building shell. However, for especially tight houses mechanical ventilation is required. Typical standards require that air leakage provides either 15 CFM per person or 0.35 ACHn, whichever is greater.
Thermal Imaging Home Inspection:
Thermal imaging helps to diagnose the problem rather than merely identify symptoms, identify and document: Electrical faults before they cause a fire, overloaded and undersized circuits, circuit breakers in need of immediate replacement, missing, damaged, and/or wet insulation, heat loss and air infiltration in walls, ceilings, floors, windows and doors, water and moisture intrusion that could lead to mold, possible pest infestation, roof leaks, before they cause serious damage, air conditioner compressor leaks, under fastening and/or missing framing members, structural defects, broken seals in double pane windows, energy loss and efficiency issues, dangerous flue leaks, damaged and/or malfunctioning radiant heating systems, unknown plumbing leaks, and overheated equipment.
This imaging technique is a powerful and noninvasive means of monitoring and diagnosing the condition of buildings. IR inspections can provide immediate documentation of as-built & post-restoration conditions, post-damaged material assessment, energy inefficiency, and electrical problems. Typically, moisture on building materials will evaporate and cool by as much as 39 degrees Fahrenheit. A wet spot (when observed with an infrared camera) is clearly visible as a distinct cool spot.
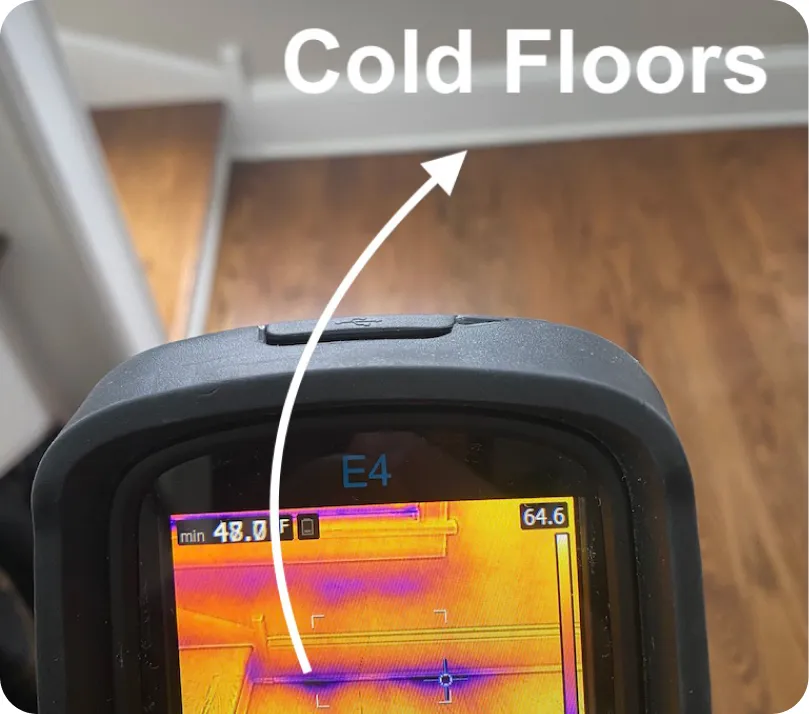
We may find significant gaps along the baseboard. We may find obvious heat escape such as can lights that have no AT rating, and usually, there will be corresponding cobwebs. We may find heat escape from top plates ( bypass between framing top plate and drywall seam).
Thermal Scan targets the exact location of air intake from the exterior and recommends a treatment solution for exterior sealing. We can prioritize treatment, and create an action plan with prices and individual line items for treatment.
Some items can be performed by our attic insulation team, while others require a handyman, painter, siding contractor, or another specialist in the respected field.
The auditor will locate unintentional air leakage and provide a solution. There are many variables to air sealing, both interior and exterior products, and application methods. For example, if the floors are wood and the trim is white ( common decorating style 2010- present) clear caulk will be used on that seam, while the seam between the base shoe and base trim will be white caulk.
Drafty cold spots can be identified without a blower door test.
Two proven facts, where there is air infiltration / heat escape, there is cobwebs / and or cracked caulk and paint around cometic seams. The caulk or paint is the last line of defense against air intrusion, and due to temperature differences, it is inevitable.
Visit after visit, house after house, same indicators, same information, same proof. Green Attic starts with an exterior property walk. We locate impactful unintentional gaps in the building envelope. Example, window frame to siding / brick not caulked.
Sometimes it is missing, sometimes it is cracked, sometimes it is poorly applied / partially applied. The resulting air intrusion comes through the path of least resistance (think water / energy) such as wall outlets and most commonly base shoe / baseboard trim.
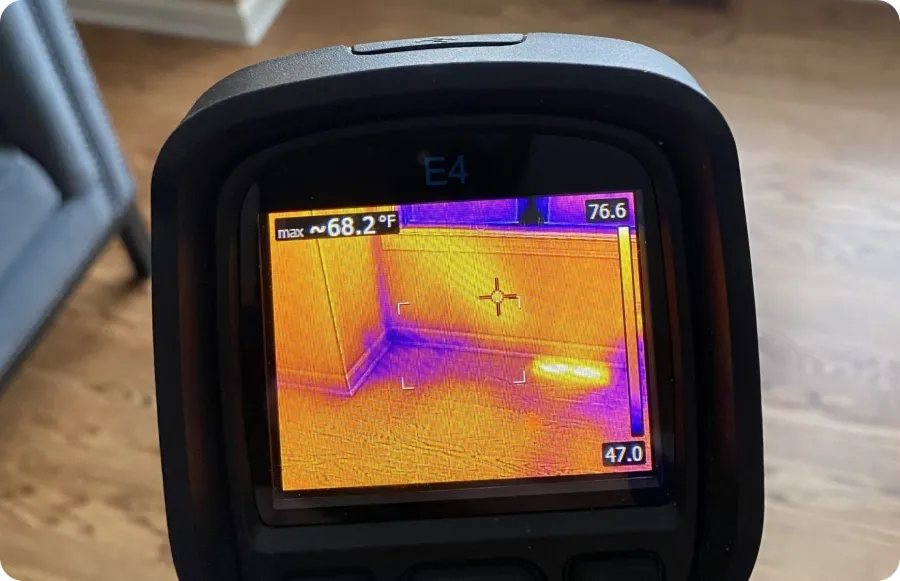
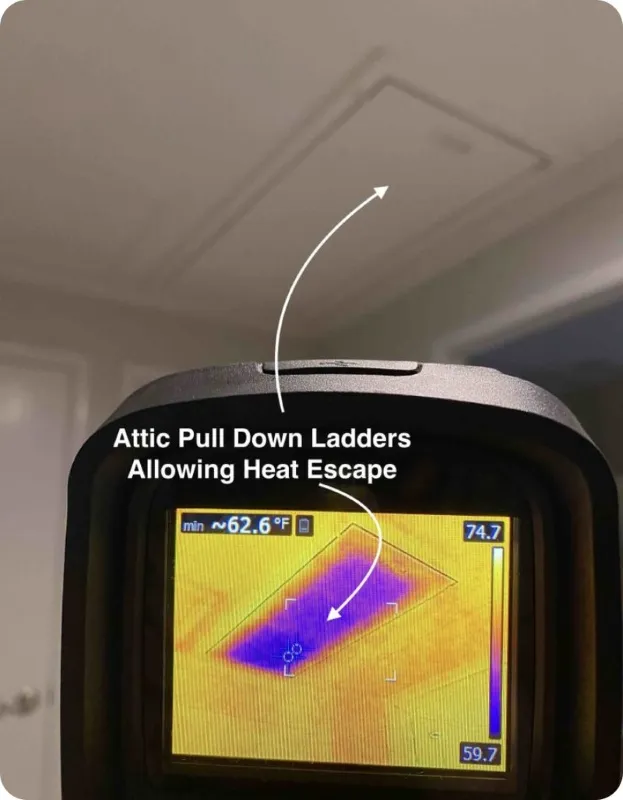
Air Leak Detection = Air Leakage Reduction Plan
✓ Green Attic focuses on the customers concern, the reason for the call, so the general items listed on a typical audit may or may not take center stage during the audit. The homeowner relies on us to direct the conversation towards truth, fact based building science, and energy conservation.
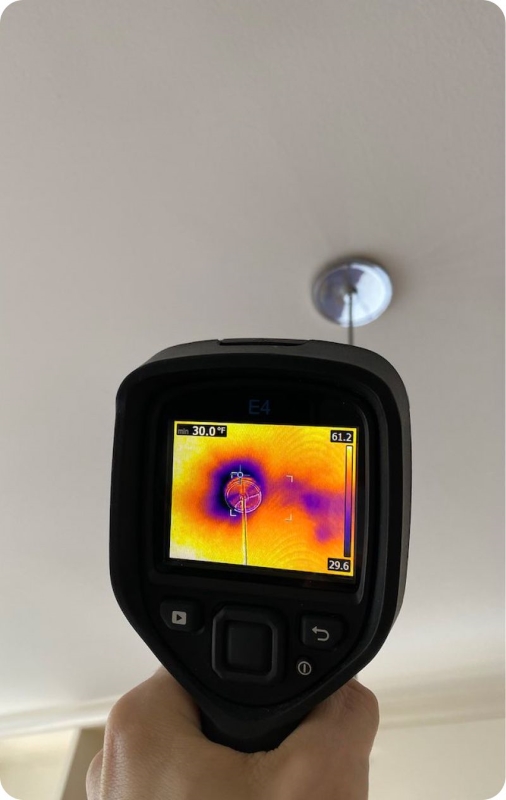
Save Up to 30% On Your Heating Bill
✓ Additionally, Green Attic will take a CFM (cubic feet per minute) reading to measure how many cubic feet ( about a basketball in size) of air is being drawn through the blower door test fan while depressurizing the home to 50Pa ( pascals). Most homes in the Chicagoland area which have average deficiencies test between 8-12 ACH.
With 4.0 being the baseline for occupancy of a new home, we are 2-3 times leakier than intended, translation to 2-3 times less comfortable, 2-3 times higher heating and cooling costs, but that is subject to other relative variables such as insulation, building construction methods and materials and more.
Several forces drive the air movement through the building shell:
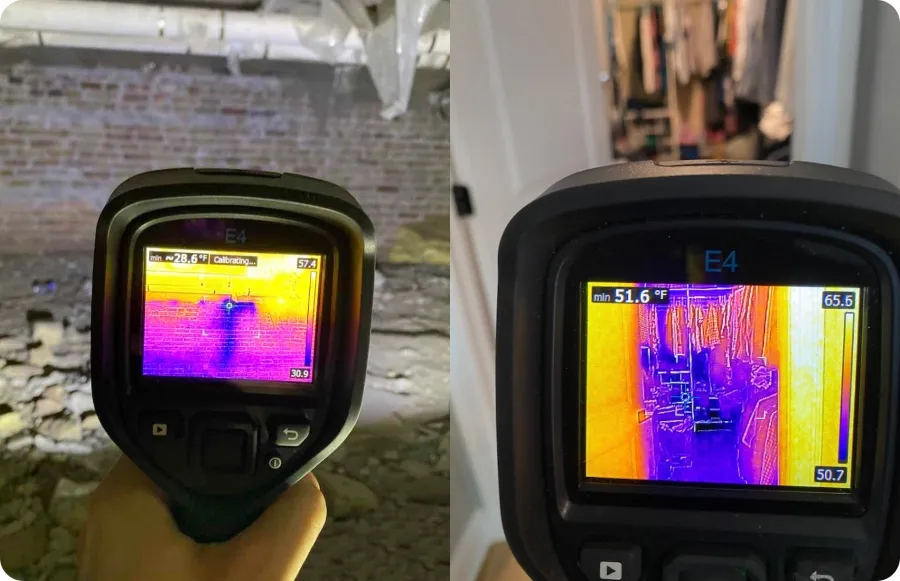
This forces cooler air to be drawn into the house at lower levels. The stack effect pressures are greatest at the highest and lowest points in the building. Therefore, a hole in the basement or attic will allow more air infiltration than an equal-sized hole near the middle of the house.
Then, using well-established formulas, an estimation of the natural air changes per hour is given. These formulas take into account the average temperatures and wind speeds in an area (colder and windier areas allow more air leakage), the building’s height (a taller building allows more leakage), and the shielding of the building against the wind (the better the shielding the less wind and then the less air leakage).
The natural air change rate is denoted by ACHn or just ACH. For example, an ACH of 0.5 means that every hour 50% of the air in the house is changed due to air infiltration. Of course, this air coming in must be heated by your furnace or boiler.
However, gas-burning appliances that are sealed combustion avoid much of the chimney pressures because they use outside air for combustion and vent the combustion gases through sealed vents.
These appliances don’t rely on any air from inside the house to create the draft necessary to vent dangerous combustion gases to the outside. Duct pressure: The furnace or A/C blower circulates air through the system’s supply and return ducts.
If the ducts are leaking, or if return air (air meant to return to the blower to continue the cycle) is restricted, rooms may have a high positive or negative pressure, which can help to drive air through the building shell.
These pressures are often large enough to double or triple the building shell’s air leakage compared to when the blower is off.
These pressures are often large enough to double or triple the building shell’s air leakage compared to when the ducts are properly sealed and the return air flow is unobstructed.
A Home Energy Assessment will assess the condition of your ductwork, identify any leaks or restrictions, and provide recommendations for improving the efficiency of your heating and cooling system.
By addressing ductwork issues, you can significantly reduce energy waste and enhance the overall comfort of your home.